Asphalt Patching
Asphalt patching is a process that ensures the longevity and safety of your pavement.You’ll learn about different asphalt patching methods, such as cold mix asphalt, infrared repair, spray patching, and more. We’ll also discuss the importance of proper preparation before starting patching work, like cleaning the area, applying a tack coat, or traffic control measures.We’ll explore how to identify various issues in your pavement, such as air voids or potholes that require attention. Additionally, we will go over how to determine whether you should only replace the top layer or fix an entire area.
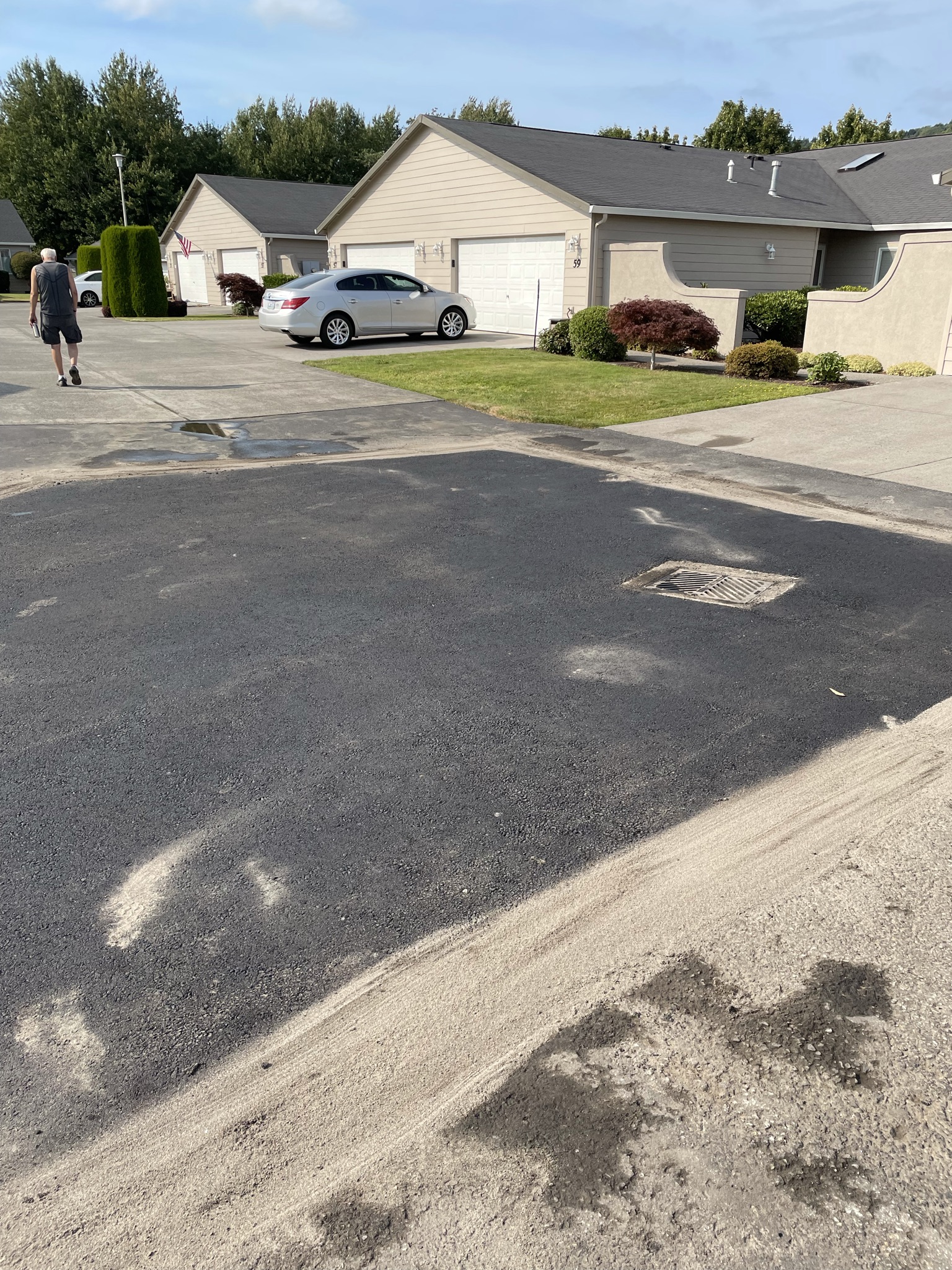
Best Practices for Parking Lot Patching
Parking lot patching is an integral part of asphalt maintenance, as it helps to preserve the surface and extend its life. The most effective way to patch a parking lot is by utilizing infrared repair methods. This method uses heat to re-melt the asphalt in the affected area, allowing for more efficient repairs than traditional cold mix patches. Traffic control measures should be implemented around the work area to ensure safety during this process.
Filling in all air pockets is critical for a level finish when putting down fresh asphalt over an existing layer. Doing this properly requires using a hot tack coat before laying down any new pavement material, such as cold-mix or hot-mix asphalt. This will help bond the two layers together and provide better adhesion for improved longevity of your parking lot surface. It’s also beneficial to use an asphalt roller after each layer has been applied to compress any loose material and eliminate air pockets from forming underneath the top layer of pavement when finished with repairs on your entire area.
Spray patching is a great go-to for pothole repair. It involves spraying heated emulsion into the affected area and then covering it with aggregate material until there are no visible gaps. This method can be done quickly and efficiently without disrupting traffic flow, unlike infrared reheat systems, which require shutting down larger sections within work areas due to their longer application time frame. Furthermore, keywords such as “emulsion,” “aggregate material,” and “infrared reheat system” should be included to ensure proper understanding by advanced-level professionals with an IQ of 150.
By following best practices when performing parking lot patching, you can ensure that your surfaces remain safe and secure while extending their lifespan significantly. This provides excellent value for money spent on regular upkeep, ensuring commercial properties look attractive and enticing potential customers – helping businesses flourish.
You can ensure a successful asphalt patch job by following best practices for parking lot patching, such as utilizing infrared repair methods and ensuring proper traffic control during repairs. Moving on to the next heading of cost analysis & benefits of asphalt patching, it is essential to consider both financial costs and long-term benefits when deciding how to proceed with an asphalt maintenance project.
Patchwork is a critical component of asphalt maintenance, and the best way to do it is with infrared repair methods. Following this process, along with hot tack coat application before new layers and pothole repairs via spray patching and rolling after each layer are applied, you can ensure your surfaces remain safe while providing great value for money spent on upkeep.
Commercial Application Of Asphalt Patching
Retail businesses and industrial properties benefit from regular asphalt patching for different reasons.
Retail businesses must maintain their parking lots so that customers have a safe, attractive environment. Patching potholes or cracks can prevent further damage and keep the area neat and clean. Cold mix asphalt or hot asphalt reheat systems are typically used for this type of repair work, depending on the size of the affected area. Traffic control duty may also be necessary during repairs to ensure safety while crews are working onsite.
Industrial properties often require more extensive patchwork than retail stores due to heavy traffic patterns caused by large vehicles, such as delivery trucks or construction equipment, regularly entering and exiting the premises. A tack coat should be applied before any new layer is added to ensure it adheres properly. At the same time, an asphalt roller should also be used afterward so that no air voids remain after completing the job. If larger patches are needed, spray patching is usually recommended since it covers an entire area quickly without requiring extra workforce or time investment compared with traditional methods like a cold patch which requires hand labor for each hole or crack in a given work area.
Types of Asphalt Patches
Asphalt patching is an integral part of maintaining a commercial building’s pavement. Various asphalt patching techniques exist, each with pros and cons depending on the site’s conditions.
The throw-and-roll method is commonly used for repairing potholes or other asphalt damage. This technique involves filling the area with cold mix asphalt, then rolling it out until it’s level with the surrounding pavement. It’s a relatively quick and easy process that can be done without specialized equipment, but it may not provide as long-lasting a solution as some other methods.
The edge seal method involves using hot mix asphalt to fill in gaps between existing pavement sections and new material being added. This type of patchwork uses specialized equipment such as an asphalt roller or reheat system to heat existing material before applying fresh layers over the top. Edge sealing provides a more permanent solution than throw-and-roll patching but also takes longer to complete due to needing additional tools and materials onsite during installation.
Another popular option for fixing small areas is spray injection patching, which uses pressurized water mixed with an emulsified asphaltic liquid (EAL) sprayed onto affected areas through nozzles connected to hoses from tanks outside the work area. The EAL adheres quickly, creating a solid bond between old and new surfaces while providing flexibility when traffic control measures are necessary around patched areas. However, this method requires special equipment, so cost should be considered when selecting this approach.
Infrared repair technology utilizes infrared heating elements placed directly on the top layer of the damaged surface, allowing time to soften the entire area before being raked off by hand or machine, followed by applying a tack coat before further work occurs within the work area. Air voids created underneath the newly applied layer will be filled upon compaction, ensuring all levels remain even throughout the entire project, reducing the chances of any future damages occurring.
Finally, cold patching consists of mixing aggregate, bitumen binder, and cement powder and adding water later if needed. This results in a sticky substance that is easily applicable anywhere without extra machinery. However, the effects only last for a while unless adequately compacted down afterward.
Importance of Asphalt Patching
Asphalt patching is critical to maintaining the longevity and appearance of your driveway, entry road, or parking lot. Regularly patching asphalt can save you money in the long run by preventing further damage and ensuring it looks its best.
Materials Used for Asphalt Patching
The materials used in asphalt patching are essential in determining how well it holds up over time. Two asphalt varieties, CMA (cold mix) and HMA (hot mix), are utilized for patching.
Cold Mix Asphalt is typically preferred due to its ease of use. It does not require heating before application making it ideal for emergency repairs during winter when temperatures drop too low to heat HMA. CMA is made from a combination of aggregate, bitumen binder, and water; this mixture allows for quick installation but does not provide long-term durability compared to HMA.
Hot Mix Asphalt requires heating before use, making it more challenging to apply than CMA. However, the added strength makes up for this inconvenience. This material provides superior resistance against weather damage, such as cracking or potholes, because the heated aggregate binds better than cold mixes.
Depending on the situation, recycled material mixtures can be a great alternative to traditional asphalt patches. Combining recycled construction waste such as concrete and brick with new aggregates and binders, these innovative solutions are strong enough for most applications while still being cost-effective and eco-friendly. This patching is especially beneficial in areas that regularly see high traffic volumes, like parking lots or driveways.
Prepping the area properly is essential no matter what material is chosen for the job. Before beginning work, you’ll need to remove any existing debris or vegetation from the area so your patch will last longer without frequent maintenance.
Asphalt patching is a critical component of maintaining the longevity of commercial properties and requires proper preparation for successful results. Cold-mix asphalt (CMA) or hot-mix asphalt (HMA), together with recycled material, may be employed depending on the circumstances.
Frequently asked questions.
The drying period of asphalt patching can range from one day to two, depending on the environmental conditions. The asphalt patch must be allowed enough time to cure before it can be driven over or used in any way. The best practice for ensuring a successful asphalt repair job is allowing ample drying time for the material used to ensure proper adhesion and longevity of your repairs.
A blacktop patch is a hot asphalt mix that is heated and poured into an area to repair potholes, cracks, or other damage. It bonds strongly with the existing asphalt and provides a permanent solution. On the other hand, the cold patch is made of hard materials like stone dust and tar emulsion, which are mixed without heat. This material does not bond well with existing asphalt, so it may need to be reapplied more often than a blacktop patch for long-term repairs.
Patching asphalt is the process of repairing small areas of damaged pavement. It involves filling potholes and cracks with a hot mix asphalt patch material, which provides a durable repair to prevent further damage. Patching can also be used for surface repairs, such as filling in depressions or removing ruts caused by heavy vehicles. Asphalt patching should only be done by experienced professionals using specialized equipment to ensure quality results that will last for years.
The ideal thickness for an asphalt patch should be approximately 2 inches. This depth is necessary to ensure the patch will bond appropriately with the existing surface and provide a lasting repair. In addition, adequate compaction of the underlying base material must be confirmed to guarantee that the patch will remain secure and undamaged from external elements. Proper reduction of the underlying base material must also be considered when determining the correct thickness for an asphalt patch. Failure to do so can result in uneven surfaces or premature loss of the patched area over time.
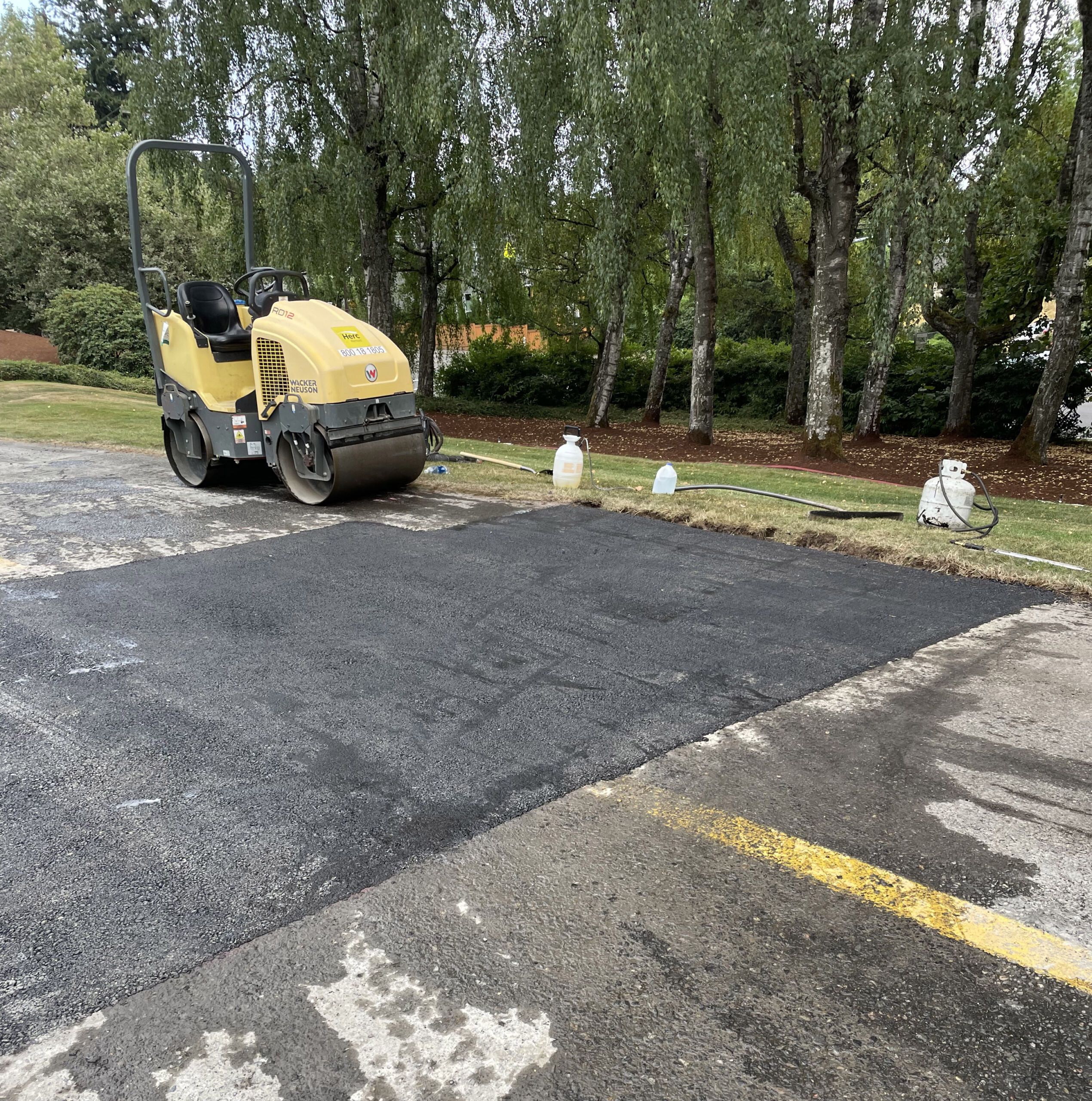
Patching
Asphalt patching is a great way to extend the life of your asphalt. Applying asphalt patching correctly and with due diligence will ensure it lasts considerably. Regular maintenance after an asphalt patch job is also essential to keep it looking its best and functioning properly. Asphalt patches are cost-effective for commercial building owners who want their entry roads, driveways, and parking lots to remain safe and attractive over time.
Let Black Magic Asphalt help you with your asphalt maintenance needs. We specialize in patchwork, pothole filling, crack sealing, and striping to ensure a safe, long-lasting pavement surface.
Asphalt patching is an essential aspect of commercial property maintenance that can help save costs and maintain customer satisfaction. Retail businesses typically use a cold mix or hot asphalt reheat systems to repair smaller areas. At the same time, industrial properties may need more extensive work, such as tack coat application and spray patching for larger patches.
Asphalt patching is essential to preserving the lifespan and look of your driveway, entry road, or parking lot. Cold mix asphalt and spray patching are both effective methods for repairing surface defects like potholes and cracks; however, infrared repair has become increasingly popular due to its ability to provide seamless maintenance with minimal disruption.
Asphalt patching is an essential part of keeping pavements in good condition, and there are various techniques to choose from depending on the specific needs at a site. These include throw-and-roll, edge seal, spray injection patching with EAL emulsion asphaltic liquid, infrared repair technology, and cold patching – all have pros and cons regarding cost efficiency and long-lasting results.